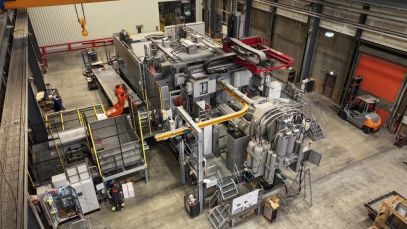
Two years ago, the development of an innovative die-casting process began, in which Handtmann invested millions. This significant investment marked the beginning of a project that could immensely change automobile production. On October 25, 2024, the first series part was cast on the new megacasting machine. Europe’s largest family-owned light metal foundry has not only demonstrated its innovative strength but also paved the way for a new era in the production of large structural parts.
Megacasting refers to the casting of very large metal parts that require special casting techniques and machines. This technology, which is particularly on the rise in China and the USA, could fundamentally change the manufacturing process of automobiles.
Handtmann’s entry into Megacasting production
By commissioning a Carat 610 extended with 61,000 kN clamping force and a shot weight of up to 128 kg of aluminum, the company is entering the production of large structural parts. This enables the production of large battery housings and complete front or rear sections for electric vehicles. Initial projects with german automobile manufacturers have already started.
The investment in megacasting underscores the company’s entrepreneurial commitment and innovation orientation. This technology is a central component of the strategy to support customers in their transformation and to strengthen the competitiveness of the german automotive industry. Investments in new processes and technologies are crucial for long-term growth and innovation.
Benefits and sustainability
The benefits of megacasting include reduced manufacturing complexity, lower procurement and logistics costs, and weight savings in the body, which is particularly important for electric vehicles. Additionally, labor-intensive joining and post-processing steps such as welding and milling can be skipped. This technology also offers advantages in vehicle recycling, as larger parts made from a single material are more sustainable.
Voices from the management
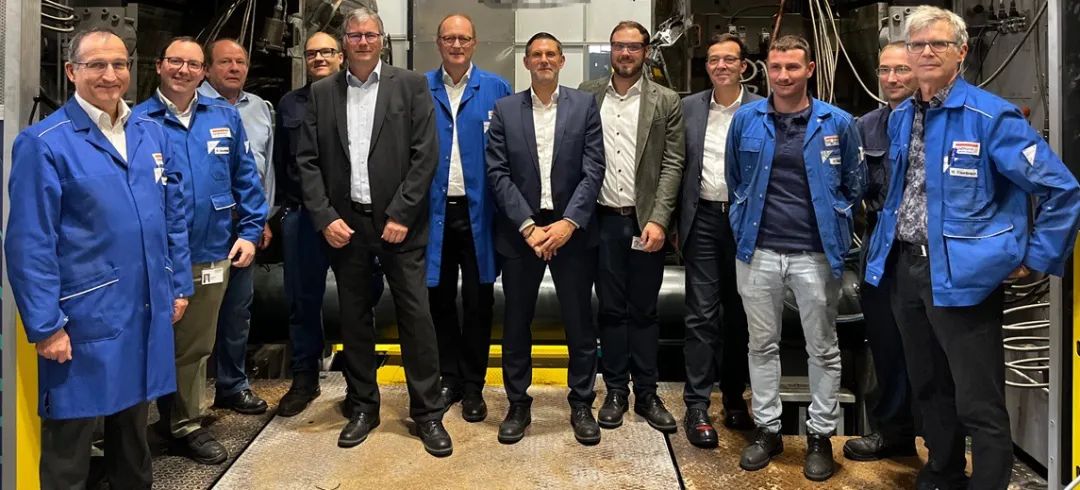
Dirk Seckler, Managing Director of Sales and Technical Development, emphasizes: “We recognized early on that we need to transform from a pure ‘built-to-print’ supplier to an innovative competence and solution provider. By entering megacasting, we are taking on a pioneering role and are the competent partner for our customers in the transformation of the automotive industry.”
Heiko Pfeiffer, Managing Director of Production, adds: “The introduction of megacasting marks a turning point in vehicle production. Large and complex structural parts can be produced in a single cast, reducing production time, improving material efficiency, and increasing the structural integrity of vehicles.”
Heiko Pfeiffer, Managing Director of Production, adds: “The introduction of megacasting marks a turning point in vehicle production. Large and complex structural parts can be produced in a single cast, reducing production time, improving material efficiency, and increasing the structural integrity of vehicles.”